Objective:
Develop and implement a rule-based methodology for ship design and material selection.
Summary:
The World Class Material Standards project targeted a fivefold increase in the throughput of preliminary designs and cost estimates that a shipyard can produce in response to market inquiries. The goal was a 33 percent reduction in cost and cycle time for pre-production processes during the contract, transition and detail design phases. The rule-based methodology, Common Item Database, standards and parametric design tools are applicable to the U.S. shipbuilding industry at large.
The overall goal was to develop a contract design process that enables a shipyard to respond quickly to customer inquiries and develop contract design packages, including cost estimates, which in addition to quick response have minimum risk to the yard in terms of price and schedule. “World Class” shipyards accomplish this by either having a limited product range (ship type) or by having a substantial experience-based set of previous contracts. Since U.S. shipyards are not in either position, this design approach is necessary to become competitive. Additionally, the goal was to develop the process so many contract packages can be developed without increasing the design work force.
A part of the design process is rapid identification of interim products, including equipment and components. For non-specified items, inclusion in the Common Item Database implies the ability to establish supply chain relationships, so shipyards and suppliers are in continuous communication about preferred equipment and components, current features, price and availability.
For specified items, the opportunity to develop Lean interim products that are reusable over many contracts and ship types offers the opportunity to reduce cost and improve competitiveness. The Common Item Database has been populated with more than 650 products, 730 suppliers and 740 product types in 45 different categories.
Developing a set of nationally recognized material and design standards allows for rapid response to customer inquiries while remaining cost competitive. This process assures that best practices standards in manufacturing are also used in design. More than 1,200 standards submitted by project team members are under continuous review and evaluation. More than 960 steel and outfit standards have been delivered.
Parametric design rules aid the designer in choosing from among many design options to rapidly drive the design process to cost competitive choices. The design tool set also offers the potential for automation (in part) of the design process. In particular, the contract design process is improved if rapid, easy, user friendly tools are available for the upfront naval architectural work (hydrostatics, stability, structure, etc.).
In the last year of the project, the team focused their efforts on developing education and training modules that were released as either introductory or application modules. Introductory modules are PowerPoint presentations, intended to introduce material in a general way. Application modules also have PowerPoint presentations, but are accompanied by a substantial workshop-style exercise. These exercises are designed to aid students in understanding how to perform design using the approach and tools developed by the project.
Final Report – Approved for public release; distribution is unlimited
Overview
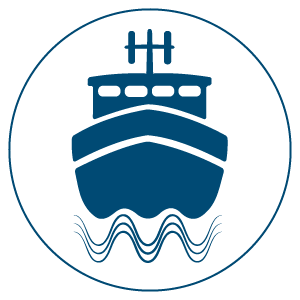
Project Team:
- General Dynamics NASSCO
- General Dynamics Bath Iron Works
- General Dynamics Electric Boat
- VT Halter Marine
- Ingalls Shipbuilding
- AMSEC, LLC
- Proteus Engineering
- VIBTECH
- First Marine International
- Munro & Associates
- ABS Americas
- SPAR Associates
- Hopeman Brothers
- Integration Partners
- University of Washington
- Webb Institute
- University of Michigan
- SIMSMART, Inc.
- Designers and Planners, Inc.
September 1999 - September 2004
NSRP ASE Investment: $9.54M
Industry Investment: $13.7M