Objective:
Define, demonstrate, and provide examples of approaches to reduce the time and cost of creating computational analysis models for shock, acoustic and stress simulations. In particular, the focus is on very large models often representing full-scale ships and Naval vessels.
Summary:
Expanded use of modeling and simulation (M&S) tools to reduce costs associated with current ship structural testing and analysis has been identified by the Navy as a key area of interest. The primary motivation of this project is to perform Computer-Aided Engineering (CAE) analysis earlier in the overall process, provide systematic data handling and process flow, allow the sharing of data and models among various disciplines, and integrating the overall CAE process. An additional objective is that of facilitating and performing more analytical simulations in lieu of very expensive, and environment unfriendly, full ship shock trials or tests.
This project was conceived and defined at the outset to accommodate the analysis modeling needs of both surface ships and submarines. In this way it is believed that common tools and approaches, or middle “ground”, could be accommodated as well as unique needs, tools, or methods which may pertain only to either submarines or surface ships. The effort expands this technology and provides for insertion and interaction with the multi-year DoD CREATE (Computational Research and Engineering Acquisition Tools and Enhancements) program and provides for shipyard test and evaluation of the developed tools. This interaction ensures that processes and tools developed as part of the NSRP M&S efforts and CREATE can be installed, implemented, and executed at major shipyards
Efforts have concentrated on reducing the time/cost of analysis during product design and process improvements. Different Computer-Aided Engineering (CAD) and CAE software codes are employed at the various industrial and Navy organizations involved in full-ship modeling and simulation activities. This project is examining new software applications to replace one or more legacy applications in the analysis workflow. Project participants have examined improving the analysis tools and process without making wholesale changes to the way organizations operate today.
The reduction of time/cost for developing large, complex computational models has been realized; however, more importantly, the project has identified and implemented broader organizational process improvements that have: allowed the use of cost-based tradeoff studies early in the design process, maximized design data reuse, minimized computational model generation time, maximized the use of design data earlier in the process, and aligned computational tools, processes and facilities to sustain effective collaboration across ship design functional areas.
At the conclusion of Phase 2, the tools developed by the project team have enabled a 50% reduction in the time required to generate a full-ship analysis model, and reduced by 25-95% the time required to perform several engineering analyses. The process improvements, insights and lessons learned during the M&S efforts can be applied to both 1st-tier and second-tier shipyards.
Key Deliverables / Benefits:
Request Final Report from NSRP – Limited Distribution authorized to U.S. shipyards and NSRP ASE Program representatives
Overview
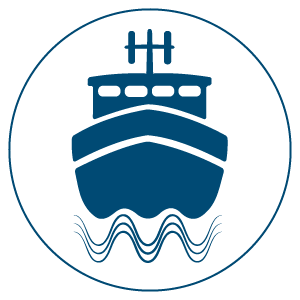
Project Team:
- General Dynamics Electric Boat
- Ingalls Shipbuilding
- Dassault Systemes Simulia Corporation
- Technosoft
- Product Data Services Corporation
- Altair
April 2008 - August 2013
NSRP ASE Investment: $4.05M
Industry Investment: $4.05M