Objective:
Project goals are to:
- Examine and test the use of digital filtering methods as a means for identifying components as candidates for collaborative robotic cutting and welding (cobot) applications using the digital ship-model (serving as a production planning tool to help optimize build strategies).
- Foster collaboration between Production Planning and Ship Design personnel in the development of digital tools and processes to help realize the potential of cobot technologies in shipyards.
- Expose the need for a coordinated “Design for Cobots” and “Plan for Cobots” analysis tool within the digital platform (digital ship-model), to reduce costs in production engineering / construction.
- Outline the technical information requirements (general specifications and standards for both commercial and naval shipbuilding programs) and a hierarchy for digital filtering tools that can provide visibility to help accelerate cobot adoption by the industry.
- Manually Beta test the project derived digital filtering method(s) to the extent possible without engaging in any significant software development activities on the project.
- Present a high-level, longer-term vision for “auto-identifying” cobot welding and cutting opportunities within the digital ship model at the ship design and the production planning stages.
Summary:
The advent of the introduction of cobots into the U.S. Shipbuilding and Repair industry is coming. Cobot welding and cutting systems have already been successfully introduced to many industries. Because of the complexity and scale of the products built by the NSRP community members, even the simple introduction of this technology into shipyards can be a complex, overwhelming task.
In order to help prepare for the eventual broader adoption of cobots into shipyards, there is a need for a process that helps ship designers “design for cobots” and production planners “plan for cobots” using product information contained in the 3D ship model and a digital filtering method to help identify cobot applications. This project will provide insight so that shipbuilders (and software vendors to the industry) can align, filter, and manage digital ship model information that allows designers and planners to do their part in accelerating the adoption of cobots. Without digital filtering tools, cobot automation adoption and the benefits of cobot cost reductions to the industry will likely remain limited and sluggish.
Welding and cutting cobots have the potential to increase productivity, help enable scalable production capacities, and reduce costs associated with component fabrication, rework/repair.
Key Deliverables / Benefits:
The Business Case for Cobot Welding Systems is very straightforward. It is built on the premise that a manual welder can work side-by-side with the Cobot welding system with both arcs producing welds simultaneously. The average Arc-On Time for a manual welder can be added to the average Arc-On Time of the cobot system to realize dramatic gains in Arc-On Time productivity. In many cases, a Cobot system operator or welder can operate several cobot welding systems in a well-designed “cell” while tacking and fitting parts themselves to greatly magnify savings. By developing the digital infrastructure for designers to rapidly assess their efforts to design ships for greater cobot use in production, and production planners to rapidly identify where cobots can be used in production for existing designs, the likelihood of future success in cobot welding and cutting system applications greatly increases.
Overview
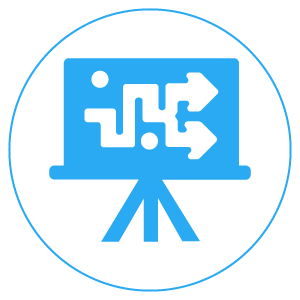
Project Team:
- Fincantieri Marinette Marine, Next Level Consulting, ShipConstructor USA
March 2023 – February 2024
NSRP INVESTMENT $150K