Objective:
To utilize recent technological advancements in ICE welding technology to improve productivity rates and reduce the construction costs of both commercial and naval vessels in U.S. shipyards.
Summary:
Ship designers are continually finding opportunities to decrease weight through the use of higher strength steels and optimized designs. This, typically, results in the use of thinner material to fabricate stiffened panels and structures to meet the requirements of the platform. Although these designs result in significant weight savings, the distortion from welding these thinner steels results in a considerable increase in cost to maintain dimensional accuracy during fabrication and subsequent construction. These added costs include special processing procedures, straightening, and rework, and may add approximately 30% to the fabrication costs of these structures.
In order to increase affordability of ships built for the U.S. Navy, alternative low-distortion high productivity welding processes must be developed, demonstrated, qualified, and implemented. To increase the productivity of welding, a process with high deposition rates needs to be employed; however, to reduce distortion, high travel speeds and low heat inputs are required. Welding processes that provide a suitable balance between productivity and distortion control need to be considered as well as provide a significant return on the equipment investment. The methods that are proposed hereafter have the potential to:
- Weld high strength steels with fewer passes and less labor
- Demonstrate consistent and acceptable weld mechanical properties at higher heat inputs
- Produce a weld thermal cycle that reduces distortion and resulting rework in thinner high strength steels
- Be robust enough to survive the demands of a shipyard / panel line environment
This project satisfied the above by investigating a breakthrough in conventional submerged arc welding (SAW) technology, called Integrated Cold Electrode (ICE), which was recently developed and made available to industry by ESAB in January 2012. The goals of this project were to evaluate ICE’s ability to enhance welding production rates, decrease distortion and costly rework, improve the properties of welds in high strength steels and therefore improve the integrity of ship’s structure.
Request Final Report from NSRP–Limited Distribution Authorized to U.S. Shipbuilding and Repair Industry and NSRP ASE Program Representatives
Overview
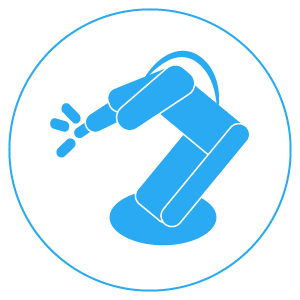
Project Team:
- BMT Fleet Technology, Ltd.
- Newport News Shipbuilding
- Marinette Marine
- ESAB
- American Bureau of Shipbuilding
- Naval Surface Warfare Center - Carderock (NSWCC)
- Defense R&D Canada
July 2013 - September 2014
NSRP ASE Investment: $376K
Industry Investment: $336K