Objective:
The objectives of this project are to develop a fast finite element analysis solver for welding sequence optimization and to apply the solver to ship structures including panel structures and complex unit structures.
Summary:
The project participants will develop a user-friendly and fast FEA solver for shipbuilding applications by leveraging Oak Ridge National Laboratory’s (ORNL) and Hexagon’s work for the automotive and nuclear industries. This solver will enable quick computation of complex material modeling that can address ongoing design and manufacturing issues in the industry. The primary use-case for the development of this solver will be weld-sequencing simulation of panel and unit assembly construction. The complex nature of weld sequencing for distortion control will allow the team to understand the current solver time and computational requirements, address existing limitations, train engineers on efficient and accurate use of the tool, and utilize Hexagon’s robust graphical user interface (GUI) to tackle the optimization of other manufacturing processes in shipbuilding and other industries. The team envisions a solver capable of replacing current analysis tools utilized to simulate welding processes to predict welding-induced stress distributions, which can be used to improve ship structural design, predict fatigue life and cracking in high stress areas, and minimize movement of alignment critical structures where hot work is required in the surrounding areas. Other potential applications include the optimization of the thermal straightening process used to correct distortion, prediction of heating paths for thermally forming curved shell plates, optimization of the hybrid laser arc welding (HLAW) process to improve toughness, and dynamic simulation of mechanical systems.
Key Deliverables / Benefits:
The minimization of weld-induced distortion of stiffened panels through optimization of welding sequences will provide significant benefit to the U.S. shipbuilding and ship repair industry, as stiffened panels comprise the vast majority of ship structural elements. As weld-induced distortion of stiffened panels is decreased, less labor for panel straightening is required, resulting in reduced rework. Downstream processes such as connection of panels to other panels in unit construction will be executed with less labor hours due to improved dimensional accuracy.
Overview
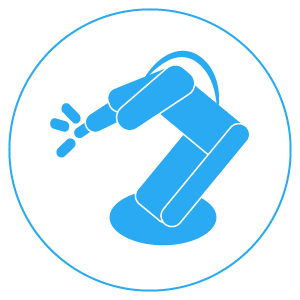
Project Team:
- Ingalls Shipbuilding, General Motors LLC, Hexagon, Oak Ridge National Laboratory, Austal USA
March 2023 – March 2024
INDUSTRY INVESTMENT: $1.2M | NSRP INVESTMENT $546K