Objective:
Develop the design software of choice for second tier shipyards (ShipConstructor) into a robust and fully integrated design solution allowing enhancements to streamline and maximize efficiency.
Summary:
A series of projects funded since 2003 have focused on the continued development of a proven 3D computer-aided ship design tool (ShipConstructor) that brings high technology efficiencies to smaller shipyards in a package better suited to them than design software employed by the first tier yards. The primary draw of the ShipConstructor design package for most second tier shipyards was the already existing core functionality, the affordability of the system, and the fact that the software runs on top of the de facto standard for computer-aided design in the U.S., AutoCAD.
Bender Shipbuilding lead a team with seven other shipyards, design agents and software developers to build a common, interoperable 3D computer-aided ship design capability through a series of modules were incorporated in ShipConstructor software. Funded modules as of 2006 include:
- HVAC – adds capability to route rectangular and round ducts, mitered corners and connectors, penetrations, etc.
- Piping – allows generation of penetrations through existing structural members, pipe spool drawings for pipe fabrication, and bills of material for parts ordering and tracking.
- Penetrations – subset that ties together the Piping and HVAC modules which identifies penetrations, links them to regulatory and design rule requirements, develops penetration lists, identify potential interferences, among other features.
- Common Parts Catalog – refinement of the ShipConstructor part specification database to accept CPC-compliant parts.
- 3D Splitting and Merging – enables design subcontractors to work concurrently with a lead shipyard on the same model, using an approach that permits splitting out a part of the 3D product model and merging it back in at a later time.
- Electrical Design (specification development) – addresses cable routing, cable hanger location, cable tray and transit loading, pinouts, and equipment connections, among others. Weld Planning specification development) – identification of welds within the model and assignment of attribute date-to-weld entities to define size, weld type (or weld symbol) and possibly weld sequence.
- FotoG Pilot – proof of concept for: 1) the development of an integrated, semi-automated production process control system, with ShipConstructor to provide real-time process control and QA for plate cutting and Unit/Block assembly; 2) true shape 3-D shell plate and 2- D shell plate expansions to improve ship repair efficiency; and 3) wet berth repairs with CAD model creation.
- NURBS Non-Uniform Rational B-Spline Surfaces – refinement of the hull surfaces definition to incorporate NURBS surfaces rather than 3-D mesh surfaces.
- As ShipConstructor Software, Inc. continues to add new modules developed through this project to its software suite, its functionality is put into use both at mid-tier yards (Bender, VT Halter, Bollinger, Marinette) and at Northrop Grumman Ship Systems for its work on Coast Guard new construction.
Final Report I – Approved for public release; distribution is unlimited
Final Report II – Approved for public release; distribution is unlimited
Overview
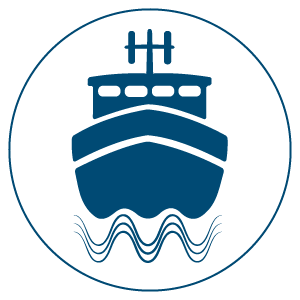
Project Team:
-
- Bender Shipbuilding & Repair
- Bollinger Shipyards
- General Dynamics Electric Boat
- Marinette Marine
- Ingalls Shipbuilding
- VT Halter Marine
- Gibbs & Cox
- Elliot Bay Design Group
- Genoa Design
- Murray & Associates
- ShipConstructor Software USA
- Albacore Research
- Anteon Corporation (Proteus Engineering)
- Alan C. McClure Associates
- Atlantec-Enterprise Solutions
- Vexcel Corporation
- ShipConstructor Software
- Knowledge Based Systems
*(Particpants represent a series of projects. Some may not have participated in all projects.)*
August 2003 - December 2006
NSRP ASE Investment: $2.84M
Industry Investment: $4.75M