Objective:
Develop best practices to achieve first-time quality using Friction Stir Welding for different combinations of alloys, joint designs and thicknesses. New non-destructive examination processes will also be developed and tested for weld evaluations.
Summary:
Friction stir welding (FSW) is a mechanized welding process that uses a rotating tool to heat the materials to be joined by friction that, in turn, results in plastic deformation, thus producing a solid-state weld. Advantages of the process include: 1) low distortion, 2) no fume production, 3) no need for filler metals and 4) no requirement for shielding gases when welding aluminum alloys. These advantages have led to FSW being used for aluminum applications in the construction of Navy ships, including: both designs of the Littoral Combat Ship (LCS); Landing Helicopter Assault (LHA); and Joint High Speed Vessel (JHSV). While the process generally produces good welds, there have been instances where the required level of weld quality has not been produced due to shortcomings in process knowledge and failure to apply quality assurance methods. These issues are inhibiting the wide scale deployment of the process and reducing affordability.
This project developed and demonstrated a body of improved process knowledge that supports the ability to make defect-free friction stir welds requiring a minimal amount of inspection.
The project objectives were as follows:
- To assure first time weld quality by developing standardized “best practice” methods and procedures for friction stir welding of aluminum ship structures
- To evaluate the full scope of potential FSW defects at varying degrees of severity and by using various inspection techniques
- To define acceptable limits of essential elements and to determine the best and most cost effective ways of identifying these defects.
The project addressed the NAVSEA and the American Bureau of Shipping (ABS) needs for:
- Definitive process test data to better define the allowable variation limits for each essential element that will lead to improved specifications and standards.
- Improved methods for inspecting production welds, to improve detection and reduce inspection time
- Improved definition of potential defects producible by FSW and their impact on ship structural performance.
The project also addressed the needs of the shipbuilders and manufacturers to improve the quality of FSW products and to minimize inspection costs by:
- Developing improved process knowledge, controls, and procedures that prevent quality problems, reduce costs, and support continued deployment of the process.
- Identifying the range of process variables that are important to producing quality welds
- Improving NDE methods to reduce weld inspection time and cost while improving inspection reliability.
By meeting these needs, the results of this project will help reduce inspection requirements, improve inspection reliability, and permit less conservative designs that ultimately reduce ship weight and costs. The body of information developed by the project team allows FSW to be performed easily, using pre-described input conditions, to make high quality welds “First Time” with minimal use of inspection.
Request Final Report from NSRP – Limited Distribution authorized to U.S. shipbuilding and repair industry and NSRP ASE Program representatives
Overview
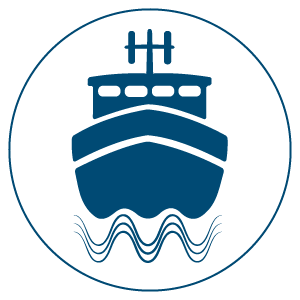
Project Team:
- Bollinger Shipyards
- Marinette Marine
- Austal USA
- Alcoa
- Naval Surface Warfare Center - Carderock (NSWCC)
- Gatekey Engineering
- American Bureau of Shipping
- Victoria Dlugokecki, P.E.
- Hepinstall Consulting
- Friction Stir Link
- Concurrent Technologies Corporation (CTC)
- Edison Welding Institute
- Manufacturing Technology, Inc.
- Tabor Industries
April 2011 - August 2013
NSRP ASE Investment: $3.3M
Industry Investment: $2.2M