Summary:
This project will refine, redesign, and productize the earlier prototype system, and perform rigorous testing to validate consistent performance of the welding system in a shipyard environment. At the end of this project, the need for mirror welding in inaccessible locations onboard the ship will be eliminated, and an alternative welding technique will be offered for use in accessible locations as well, to provide magnification and improved process control, while reducing the risk of common eye injuries. The headset will provide weld information at point of use on the video screen during welding and provide the ability for a digital recording of weld quality and process information to enable forensic analysis. This project will provide a SMART technology-enabled welding toolset to attract the “next generation” welding workforce. The system will be manufactured at an economical price point that supports adoption by shipyards.
Key Deliverables / Benefits:
- Preliminary Market Research Report
- Marketing Requirements Document and Product Requirements Document
- Architectural Specification Review
- Demonstration of Alpha System Software
- Test Procedures, Implementation, and Test Report
- Manufacturing Plan
- Project Workshop Materials, Final Report, including Implementation Status
- Training Package
Increased weld productivity will reduce life cycle maintenance cost across all maintenance and modernization availabilities, and as a result, reduce Total Ownership Cost of ships.
Overview
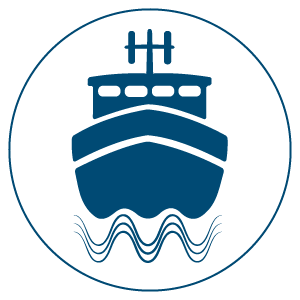
Project Team:
- Pacific Shipyards International, Fincantieri Marine Repair, Fresh Consulting, EnergynTech, D’Angelo Technologies, Gatekey Engineering, Hepinstall Consulting Group, Miller Electric
April 2023-December 2024
INDUSTRY INVESTMENT: $1,240K | NSRP INVESTMENT: $1,226K