Objective:
The objectives of this project are to:
- Early stage implementation of visual welding application on welding crawler platform for extended in-field testing.
- Develop a system ready for in-field testing and evaluation for clips and collar welding applications
- Develop a system ready for in-field testing and evaluation for erection joint welding such as during module assembly and inner bottom construction
Summary:
This Project proposes advances on a High-Mobility Manufacturing Robot – integrating mobile arm into shipyard manufacturing environments. This allows these platforms to be brought to the most common ship welds: collars, clips and erection welds. These mobile welding platforms can augment weld technicians and significantly improve productivity and safety.
Key Deliverables / Benefits:
Collars, clips and erection joints make up a large quantity of welds on naval ships. Most of these welds are performed manually, in tight spaces, among obstructions or in compartments, often out of position. Average industry arc time is around 22%, but it’s closer to 15% for these welds. Robotic welding arms run at 80% arc on time (including set up time). Addressing these welds can reduce weld costs on Navy ships by 25% or more. This project will demonstrate that the work that has traditionally been performed manually can be addressed by the combination of RTT’s mobile platforms with small robotic welding arms. The combined system will perform welds previously only addressable by human welders.
The outcomes of the project will bring factory-type automation to the welds on the ship that have yet to see automation, but yet form a majority (above 50%) of the types of welds present during the ship construction.
Targeted Benefit #1 – HMMR Robot system capable of mechanized, automated welding of selected task. The team anticipates being able to address some mechanized or automated operation in 25% of the collar/clip welding operations.
- Reduced labor cost
- Better queuing management opportunities
Targeted Benefit #2 – HMMR Robot system capable of mechanized welding. The team anticipate beings able to address 10-15% of the compartments with some level of mechanization operation.
- Increase areas to apply mechanization
- Less rework
- Less scrap
Overview
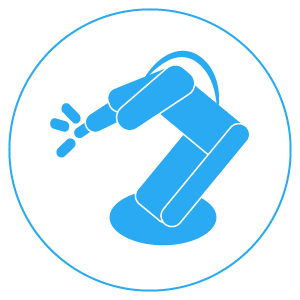
Robotic Technologies of Tennessee LLC (RTT)
Vigor Shipyards
Edison Welding Institute (EWI)
Cahill Consulting Group
Naval Surface Warfare Center-Carderock Division
March 2020 – March 2022
INDUSTRY INVESTMENT: $725K | NSRP ASE INVESTMENT $703K