Objective:
The objective of this project will be to study the various alternatives for Insulated Bus Pipe (IBP) connector types that are possible for improving cost controls and increasing commonality for shipbuilding integration. IBP currently comes with standard bolted connections. These terminal ends are commonly connected using flexible braided connectors or flexible copper laminated busbar sections. This project will look at multiple alternatives to bolted connections to include options for shock and vibration isolation such as braided copper couplings. This project will research and integrate a common interface with Navy Original Equipment Manufacturers (OEM) equipment to improve the implementation and transition strategy for the Navy.
Summary:
This 24-month project will be focused on an initial meeting with each OEM and GD BIW to research and evaluate the various interconnections required for a diverse set of electrical equipment onboard Navy ships. Phase I includes the research and decision upon a common IBP connector interface that can work with most electrical equipment. This phase will evaluate integration requirements (e.g. environmental factors such as EMI, shock, vibration) as the team works closely with the OEMs. Phase II will include installing short (1.5 meter) sections of the IBP into the OEM equipment at their various integration facilities around the country.
Key Deliverables / Benefits:
The team estimates the following benefits:
- Using IBP in place of the legacy 400MCM cables and performing the installation at the earliest point in the build process results in >20% savings in hours to install, connect and test.
- The estimated weight of the as-is baseline (19,812 feet of 400MCM cable) is 240.9 tons, whereas the total weight of the post-implementation (4,953 feet of IBP) is 66.9 tons, providing a 72% savings in total weight.
- GD BIW provided a conservative estimate of savings assuming that project would successfully integrate a common press fit connection method such as Stäubli’s MULTILAM standard plug connections. BIW electrical engineer, Mr. Bill Burtt estimates a 50% savings in connection time using a common press fit connection type replacing traditional bolted connections.
- An analysis was conducted estimating the installed cost of IBP and compared to the installed cost of using various types of shipboard cables. When compared to installing 400MCM cables, IBP provides an estimated 51% savings.
Overview
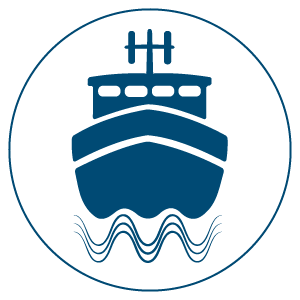
Hepburn and Sons, Tefelen, General Dynamics Bath Iron Works (GD BIW), Stäubli, RSL Fiber, Rolls Royce, and American Bureau of Shipping (ABS), Florida State University Center For Advanced Power Systems (FSU CAPS), Aero Nav Laboratories
December 2019 – December 2021
INDUSTRY INVESTMENT: $1.1M | NSRP INVESTMENT $1.1M