Objective:
Demonstrate the benefits of using laser peening within the shipbuilding industry. Laser peening (TRL 9) will be shown to improve shipbuilding manufacturing processes by strengthening components, shaping metal without using heat, and saving both production and life cycle costs.
Summary:
Laser peening uses a high energy laser fired at the surface of a metal part. Pressure pulses of one million psi are generated sending shock waves through the part. Multiple firings of the laser impart a layer of residual compressive stress that is four times deeper than that attainable from conventional peening treatments. Deeper levels of compressive stress provide greater resistance to fatigue and corrosion failures while also providing a means to form structures without using heat. Laser peening has been successfully used within the aviation industry for thirteen years.
This project will demonstrate a positive Return on Investment (ROI) through the application of laser peening in key representative shipbuilding processes such as: fatigue mitigation, stress corrosion cracking (SCC) prevention, flame straightening, forming and fit-up of metal plating using aluminum and HSLA 65; and corrosion resistance and fatigue mitigation of propulsion shafts employing Inconel cladding on HY-80. Laser peening will fundamentally change shipbuilding by reducing production cost and the time it takes for shipyards to straighten metal plate edges, conduct fit-up, fabricate complex curves in metal plates and relieve stress in heat affected zones including welds. This project will also reduce ship repair costs by extending the life of ship structures similar to the demonstrated extended lifetime of jet engine blades within the aviation industry. It is expected that laser peening will eliminate the use of flame straightening and the requirement for costly cladding on propulsion shafting to reduce corrosion.
Three problematic areas will be investigated throughout this project:
- Shipyards are currently having difficulty installing aluminum water tight doors with wavy edges and are using flame straightening to accomplish this, despite the fact that high heat reduces the aluminum’s resistance to brittle fracture and cracking
- Shipyards are currently using a costly process to prevent general corrosion of Inconel cladding on HY-80 steel of the propulsion shafting
- Shipyards are experiencing post-welding steel (HSLA 65) deckplating deflections between stiffeners that must be corrected using a time consuming heat process
Overview
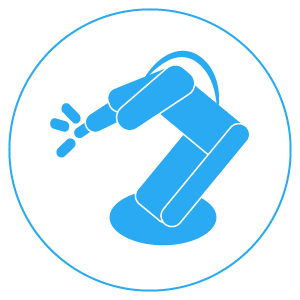
Project Team:
- Hepburn and Sons, LLC
- Curtiss-Wright Surface Technologies
- Ingalls Shipbuilding
April 2015 - June 2017
NSRP ASE Investment: $844K
Industry Investment: $425K