Objective:
Leverage expertise, technologies and best manufacturing practices from other leading-edge manufacturing industries and apply them to ship repair and conversion project.
Summary:
The objectives of this effort were to reduce cost and turnaround time, and improve overall quality for ship repair and conversion processes by identifying and applying a set of best manufacturing principles for ship check and reverse engineering processes, fabrication processes and repair/conversion as a system. One aspect of the project was to develop and implement a reverse engineering system using various pieces of metrology equipment. A review of best practices from other industries and an evaluation of state- of-the-art, large-scale measurement technologies were conducted. It was determined that no one instrument technology is right for all applications. Therefore, a total station capable of measuring arbitrary surfaces and traditional targets was selected for Atlantic Marine in Mobile, AL; while an articulated arm coordinate measuring machine was deployed at Atlantic Marine in Jacksonville, FL. Use of the total station in both infrared and reflector-less modes has led to many successful measurements for steel hull applications. Reflector-less measurements using a laser offer the best results for close range applications, because of the ease of use (no reflector targets to set up) and the precision of manual operation. If longer-range measurements are required, reflectors are set up on the object, and readings are taken in the infrared mode. An articulated arm coordinate measuring machine (ROMER arm) has proven capable of efficiently and accurately measuring flat/curved steel plate in unrestricted spaces, piping systems (existing and new pipe routes), pipe and steel during off-site ship checks and ventilation ducting. It has been able to maintain and verify accuracy during fabrication, as well as collect, store and transfer information electronically into CNC equipment. Time studies performed on the articulated arm estimate a cycle time reduction of 10% – 15% and a labor reduction of 10% – 15%. Atlantic Marine has customers that specifically request this technology because the accuracy and quality of the replication is near perfection.
Another aspect of this project was to improve worker, tool and equipment accessibility to external ship surfaces during ship repair and conversion operations in drydock. The project team focused on NIST-developed RoboCrane technology combined with commercial scaffolding to develop a joy-stick controlled “flying carpet.” Cables from a drydock’s wingwalls suspend the flying carpet, providing access to the majority of the ship’s exterior hull. While the flying carpet is not being used in production at Atlantic Marine, NIST continues to actively seek implementation sites at other shipyards.
Request Final Report from NSRP – Limited Distribution authorized to U.s. shipyards and NSRP ASE Program representatives
Overview
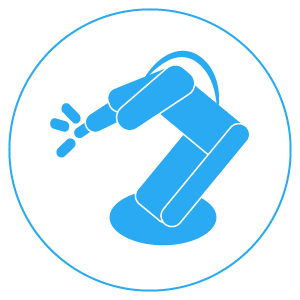
Project Team:
- Atlantic Marine
- NIST
August 1999 - September 2002
NSRP ASE Investment: $1.2M
Industry Investment: $1.2M
NIST Investment: $1.2M