Objective:
This project’s overall goal was validation of swage bulkhead behavior with outfitting/structural details incorporated into the design using non-linear FEA software compared to the data collected during physical testing to structural failure, within 25% of the FEA prediction.
Summary:
This project developed design and production guidance for integrating swaged bulkheads into other ship structure, including interfaces with the requirements of outfitting systems and standard non-swage structural elements. This was achieved through finite element analysis (FEA) of the interface areas, including openings, headers, and brackets, supplemented by physical testing as the project progresses. Integration of swaged bulkheads into existing ship systems is the best way to bring this cost-saving technology into American built ships on a large scale. This project extended the current swage bulkhead effort that will culminate by incorporating swage bulkhead requirements into the ABS Marine Vessel Rules by examining production-specific details that will improve the interface of this technology with existing shipyard methods and equipment.
Key Deliverables / Benefits:
This research project advanced swage technology by developing direct analysis methodologies to reliably predict the behavior of swaged bulkheads under various loads, thus facilitating the widespread use of swage bulkheads in future ship designs for both non-load bearing and load bearing applications. The aim is to bring U.S. shipyards closer to the goal of reducing the overall cost of ship design, construction, and ownership for all customers.
Overview
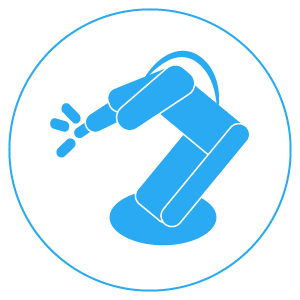
General Dynamics NASSCO, San Diego State University
May 2018 – July 2019
INDUSTRY INVESTMENT: $248K | NSRP ASE INVESTMENT $352K